El papel de los turborodamientos en la mejora de la eficiencia en las tecnologías actuales y futuras
By Cummins Components Business Unit
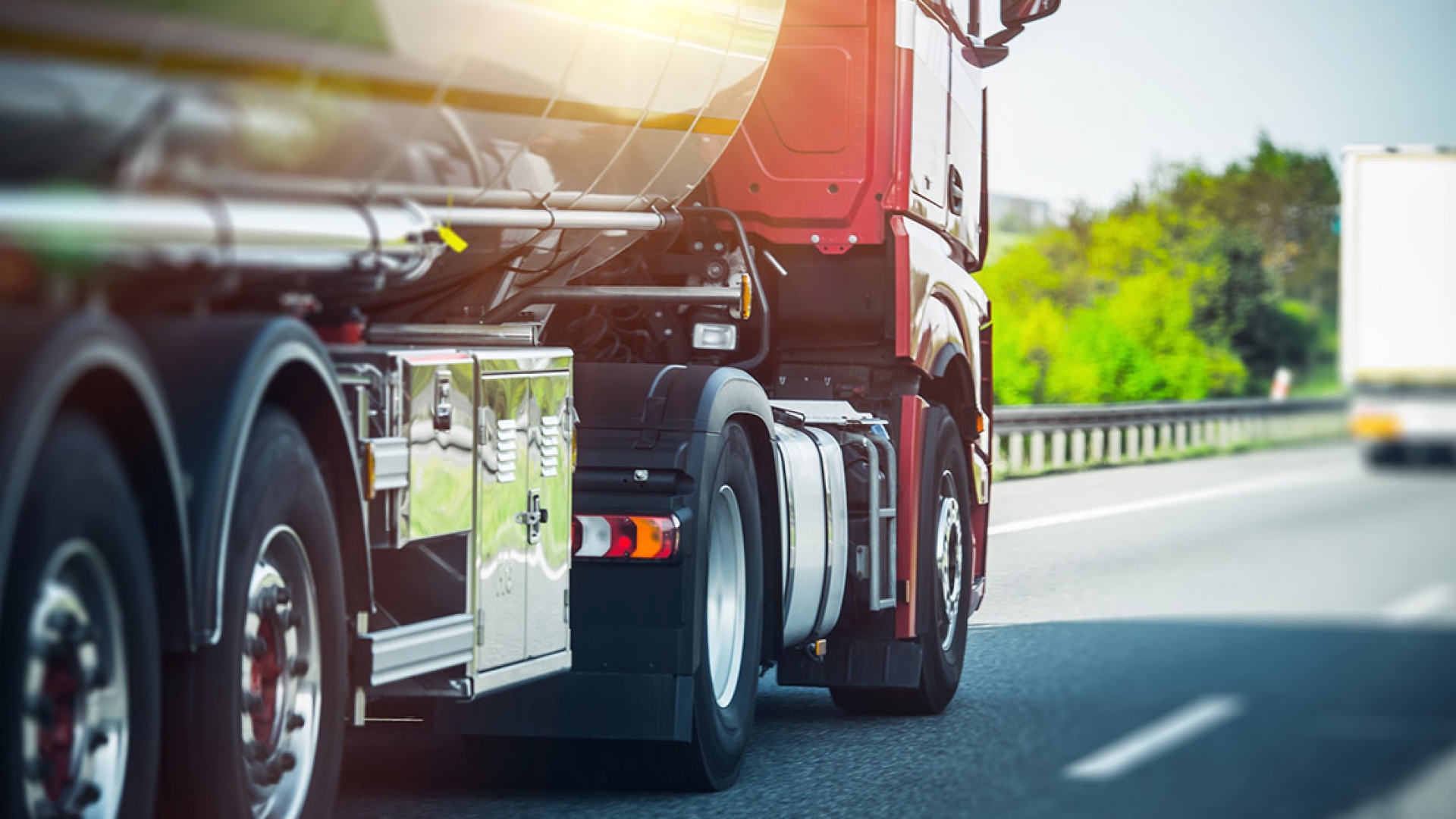
Cummins Inc. está comprometida con la sostenibilidad y la administración ambiental al enfocarse en tecnologías innovadoras, eficiencia operativa y esfuerzos de colaboración. This comes through Destination Zero - Cummins’ strategy for reaching zero emissions. This path will require innovation and advancement in every component to deliver powerful and reliable products to our customers that help them meet and exceed environmental regulations.
We have discussed the advancements in turbocharger technologies, including the different types of turbochargers that Cummins can provide to our customers, for a wide range of applications. Another key component that has seen advancement and innovation are turbo bearings. Turbo bearings are components that support the turbocharger and are integral to maintaining the efficiency and reducing emissions in turbochargers.
Turbo bearings play a significant role in ensuring that turbochargers perform reliably and efficiently. They control the high-speed rotation of the turbine and compressor wheels while minimising friction and wear. These crucial components of turbochargers ensure longevity and enable high performance and efficiency.
With the great shift in commercial transportation technologies, a new generation of turbocharger technologies will play a role in servicing the unique needs of vehicles powered by alternative fuels and fuel cells.
Cummins Inc. has found remarkable success in using the cold testing method to test its turbochargers.
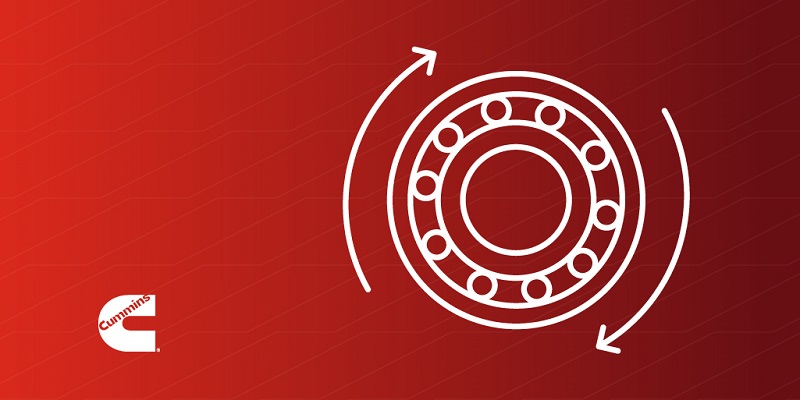
Role of turbo bearing technologies in internal combustion engines (ICE)?
In ICE vehicles, turbo bearings are used to support the rotating components in a turbocharger. A turbocharger has two main components: a turbine and a compressor. The turbine is driven by exhaust gases leaving the engine and the compressor squeezes the intake air before it enters an engine’s cylinders. To ensure the turbine and compressor operate properly, turbo bearings are used to accurately control the radial and axial motion of wheels and minimize friction losses for the components. All of this happens under extreme conditions including high speeds with low viscosity engine oils, high oil supply temperatures and gas temperatures exceeding 760C/1400F.
Today’s turbo bearing technologies fall into two main categories: hydrodynamic bearings and rolling element bearings.
Hydrodynamic Bearings (Journal Bearings):
In today's turbochargers, two "floating ring" journal bearings are the most widely used configuration. These journal bearings are also known as hydrodynamic bearings. These floating ring bearings control the radial motion of the rotor in the turbo using two oil films at the floating ring inner and outer diameters. They work together with the separate taper land thrust bearing which controls the axial motion.
In smaller turbochargers, you may see different types of hydrodynamic bearings, like semi-floating single piece journal bearings, or integrated single piece semi-floating bearings, which use thrust pads on a bearing’s end surfaces to carry axial forces.
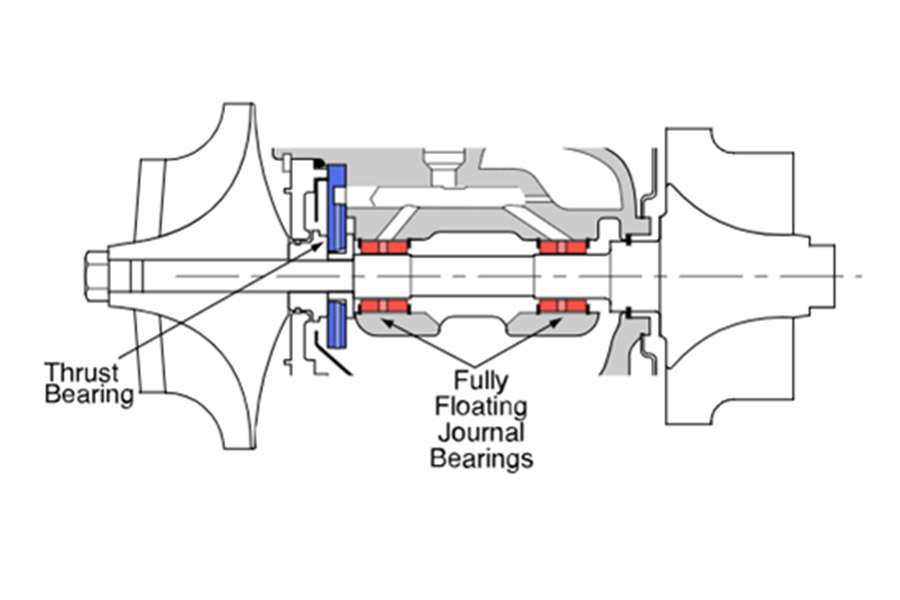
Rolling Element Bearings:
The other bearing technology used in turbochargers, rolling element bearings, have their origins in the aerospace industry. These bearings use a single bearing "cartridge" with two rows of angular contact ball bearings with ceramic balls. The cartridge manages to control both the radial and axial rotor motion in a single assembly.
An oil damper, or squeeze film, is positioned between the cartridge's outer diameter and the bearing housing to extend bearing life and control noise levels by easing the stresses on the components. Orifices in the cartridge's outer race regulate pressurized oil flows that provide lubrication for the bearings.
Click on the 'blue' spots on this interactive and find out more about advancements in turbo technology. Click on the link to subscribe to our newsletter.
Difference between hydrodynamic bearings and rolling element bearings:
Rolling element bearing can cost more, but they offer improved performance by reducing bearing losses and providing better control over radial and axial motion, which helps reduce aerodynamic clearances and lower motion levels to boost the aerodynamic efficiency of turbochargers. These rolling element bearings also enable operations when oil supply pressures are low and work with smaller power engine pumps, all while delivering higher engine efficiency.
Manufacturers have the discretion to determine whether rolling element bearing technology or hydrodynamic bearing technology is the right solution for their application. They can make the trade-off by keeping in mind that the higher initial bearing cost can be offset by engine efficiency.
Role of turbo bearings for new e-machines:
Battery electric vehicles (BEVs) and Fuel Cells Electric Vehicles (FCEVs) do not use turbo bearings in the same way that ICE vehicles do. There are, however, some specialized applications in BEVs and FCEVs where turbo bearings may be useful - even if only indirectly. For these vehicle technologies, particularly in hydrogen fuel cell turbomachines, using oil is a non-starter, as even a small leak can degrade a hydrogen fuel cell. In such cases, the preferred bearing technology for fuel cells is an oil-free, air foil bearing. Since hydrodynamic air fan bearing (AFB) use air as the working fluid instead of oil, they are much better suited for FCEVs. By leveraging flexible foils, the hydrodynamic bearings form an air film clearance that varies in response to the air pressures inside it.
As vehicle technology advances, so will components that power them. It is critical for manufacturers and fleet managers to stay updated and informed about the right components that will be needed for their applications. Turbo bearings along with turbochargers, can support alternative and future technologies while helping businesses meet their sustainability goals.
The dynamic nature of these specialized components that not only improve performance of the engines, but also help reduce emissions. No matter the fuel technology or the application, Cummins can cater to a wide range of applications and provide the most suitable equipment and parts tailored to our customer's needs.
Author Profiles
Temas relacionados
Related Tags