What is circular life cycle planning and what are its benefits?
By Cummins Inc., Global Power Technology Leader
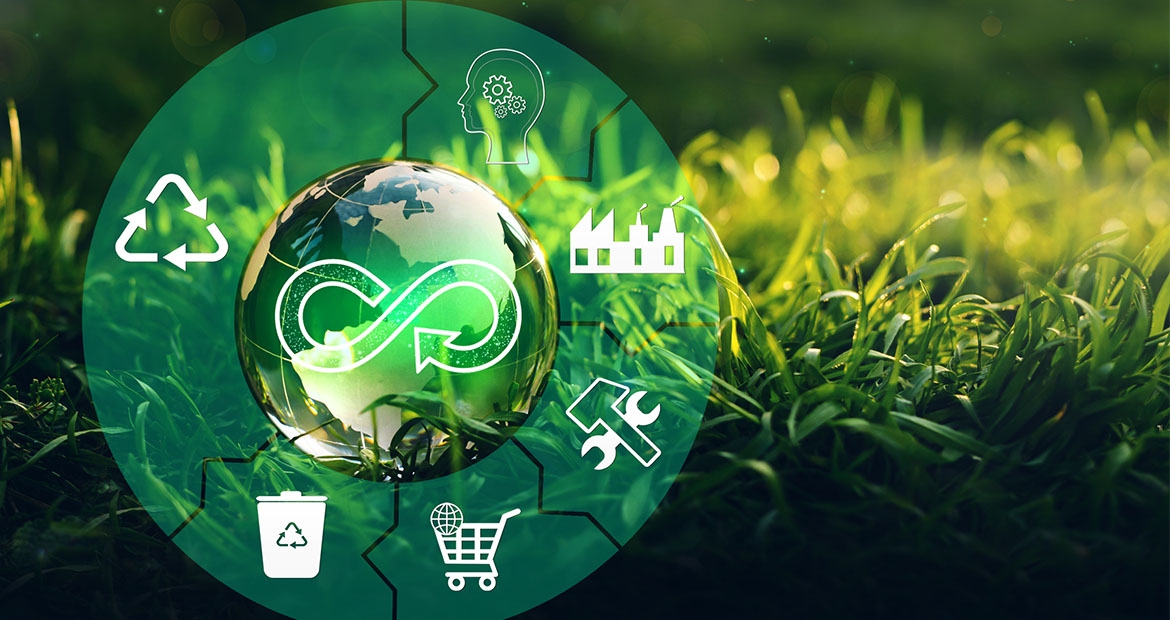
Circular life cycle planning is gaining traction as an alternative to traditional manufacturing practices. By comparing the principles of circular and linear life cycles, we can understand their implications for businesses and the environment. This article discusses the importance of circular life cycle planning, its advantages and its adoption by Cummins Inc. Let's explore the benefits and practices of this sustainable approach.
What Is The Difference Between Linear Life Cycle And Circular Life Cycle?
The linear life cycle in manufacturing predominantly follows a straightforward path: the “take-make-waste” approach. In this approach, raw materials are turned into finished products, which are then purchased and used by the end-customer. Once these products reach the end of their first use cycle, they are discarded in landfills or other waste areas. There are, however, efforts to turn landfill waste into renewable natural gas (RNG) as one of the approaches to decarbonization. In a linear life cycle, products are manufactured and delivered quickly to market, but longer-term environmental impacts are not accounted for. For instance, a piece of machinery made under a linear model might be disposed of entirely after its first use cycle, without any of its parts being salvaged and reused or the entire machine rebuilt for a next use cycle. This could mean building a new machinery by sourcing all new raw material which could not only add to material and logistics costs, but also impact sustainability goals for businesses.
The circular life cycle, on the other hand, emphasizes a more sustainable "reduce, reuse, recycle" strategy. Under this strategy, products are designed and manufactured ideally with multiple use cycles in mind. The goal is to ensure that once a product reaches the end of its service life i.e. a use cycle, it doesn't end up as waste. Instead, it can be broken down for parts that can be reused, recycled or the entire system rebuilt or remanufactured. Taking the example of the piece of machinery again, under a circular model, once the piece reaches the end of its- first use cycle, specific components can be removed and integrated into new or other working machines. The materials might also be recycled or remanufactured and used to produce new items.
This shift from a linear to a circular life cycle model not only ensures sustainability but also enhances the efficiency of resource utilization. Companies and industries that embrace the circular life cycle can potentially reduce costs, minimize waste and maximize the value derived from each product. For customers and suppliers, this means products offering them extended utility and companies demonstrating a commitment to environmental responsibility and resource optimization.
What are the benefits of Circular Life Cycle Planning?
Circular life cycle reduces the need for new raw materials:
One of the key advantages of adopting a circular life cycle approach is the money saved on buying new raw materials. For instance, some metals that are used in manufacturing can be melted down and reused to create new parts. This conserves finite resources and reduces the need to extract new raw materials. By reducing the need for continued mining of these metals and materials, environmental impact is also reduced.
Circular life cycle can help reduce logistical dependencies:
Another benefit of adopting the circular life cycle model, is the reduced pressure on supply chains. Over time, with more materials being reused or recycled, the demand for the shipment of new materials will decrease. This will not only reduce logistical considerations but will also decrease the emissions associated with transporting goods across vast distances. For example, a company that recycles or reuses metals within its operations might not need to import as much steel or aluminum, leading to fewer shipments and subsequently, fewer emissions.
Circular life cycle model helps businesses keep costs low:
Cost savings present another compelling case for the circular economy. By aligning the company’s supply chain and materials handling to the principles of the circular life cycle planning, businesses can enjoy reductions in expenses related to shipping, procuring new materials and initiating production from scratch. It’s not just the company that saves money, but end customers also benefit from purchasing high-quality remanufactured products at a fraction of the cost.
Circular Life Cycle Planning As A Part Of Sustainability Goals
Circular life cycle planning offers a sustainable alternative to traditional manufacturing methods. By moving from a linear life cycle model to a circular life cycle model, businesses can harness both the environmental and the financial benefits. Adopting a circular life cycle plan is a sensible choice for businesses aiming for sustainable growth while keeping costs down.
Cummins has embraced using natural resources in the most sustainable way as one of its 2050 aspirational targets. As part of this target, a specific goal for 2030 is to Create a Circular Life Cycle Plan for Every Part to Use Less, Use Better and Use Again. This means that when each new part is created, we will have established what its life cycle management intent is – whether it can be reused, rebuilt/remanufactured, recycled, has other beneficial use or will it be waste after first use.
Author Profiles
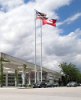
Cummins Inc., Global Power Technology Leader
Cummins Inc., a global power solutions leader, comprises five business segments - Components, Engine, Distribution, Power Systems, and Accelera by Cummins - supported by its global manufacturing and extensive service and support network, skilled workforce and vast technological expertise. Cummins is committed to its Destination Zero strategy - the company's commitment to sustainability and helping its customers successfully navigate the energy transition with its broad portfolio of products. Cummins has approximately 69,900 employees and earned $3.9 billion on sales of $34.1 billion in 2024. See how Cummins is leading the world toward a future of smarter, cleaner power at www.cummins.com.
Related Tags