Learning program helps transform operators into top-notch technicians
By Haley Allaben, Content Marketing Associate
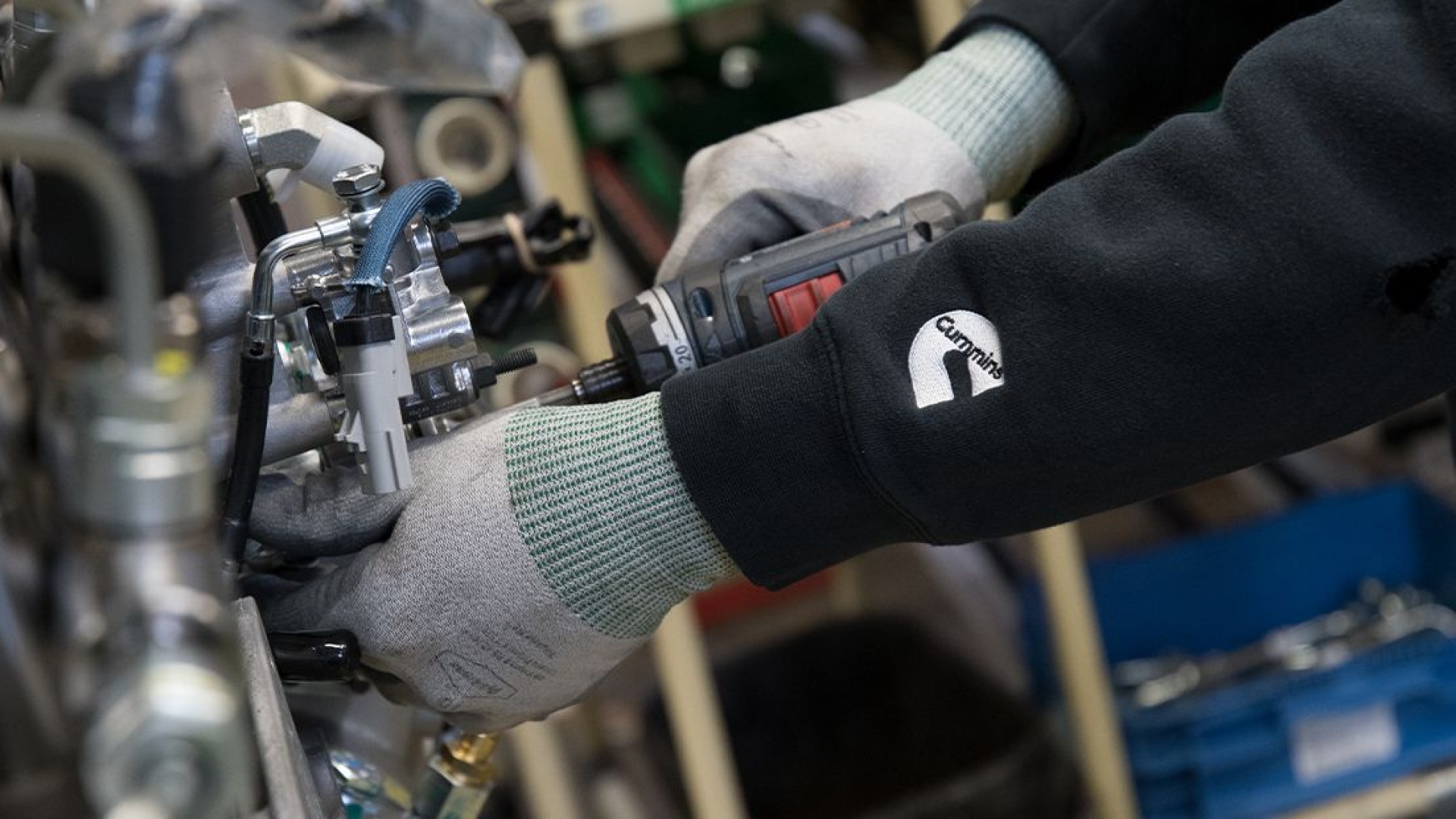
Technicians, mechanics and skilled trade workers are essential for building Cummins Inc. engines. Yet, positions like these are experiencing shortages.
In January 2023, Fortune magazine reported the alarming news that “America has a huge manufacturing labor shortage – and its education system is nowhere close to plugging the gap.” Determined to reverse the trend, Cummins Jamestown Engine Plant (JEP) and Jamestown Community College (JCC) partnered to form a program enabling employees to earn Manufacturing Skills Standards Council (MSSC) certifications.
The partnership aims to build tangible skills and professional development for JEP employees. Nickole Egger, Senior HR Generalist at JEP helps guide the program. Egger is joined by colleagues Lisa Ferguson, HR Administrator, who routinely facilitates information sessions for employees, and Jennifer Burlee, Central Services Technical Service Leader, who consistently champions and leads the skilled trainee program. Their combined passion for professional development has successfully steered the program over the years.
What is the Manufacturing Skills Standards Council?
MSSC is an industry-defined, federally endorsed program accepted in multiple industrial arenas. The program is designed to equip entering and incumbent technicians with the skills and tools to succeed as technology rapidly changes.
Available programs include Certified Production Tech (CPT), Certified Logistics Technician (CLT) and Certified Technician Supply Chain Automation (CTSCA), among others. CPT is the most popular course Cummins employees choose.
Program structure and certification pillars
Through self-paced modules online with some in-person learning, Cummins employees can make the courses work for them. Managers mentor the employee along the way. This training is not required but, says Egger, "as some of our operators look to move into the skilled trades trainee program, this is a great step to move them into that arena."
Certification covers four pillars:
- Safety and employability
- Manufacturing process and production
- Calidad
- Mantenimiento
Newfound skills benefit not only the individual employees but the company as a whole. "We can give more accountability and responsibility to the operators, freeing our technicians and engineers for those bigger things they need to be working on," says Egger.
Cummins understands the value of supporting its people. Egger reflects, "Whenever you have [programs] like this, you go, 'Am I going to be training a workforce that's just going to leave us?' But essentially what you see is, when you don't invest in your people, they're going to leave you anyway. We need to invest in our folks, and that investment for us has just led to better engagement and less attrition."
Interested in learning more? Don’t forget to check out Jamestown Engine Plant’s skilled trade apprenticeship program.
Author Profiles
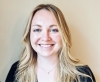
Haley Allaben, Content Marketing Associate
Haley Allaben is a Content Marketing Associate for Cummins Inc. She focuses on a range of content from diesel to employee-focused stories, fueling her passion to inform and engage. Haley began her career in nonprofit communications and project management, before coming to Cummins in 2022. Haley graduated from DePauw University with a BA in English Writing.
Related Tags