Examples of hydrogen engines in mobility and transportation
By Jim Nebergall, General Manager of the Hydrogen Engine Business
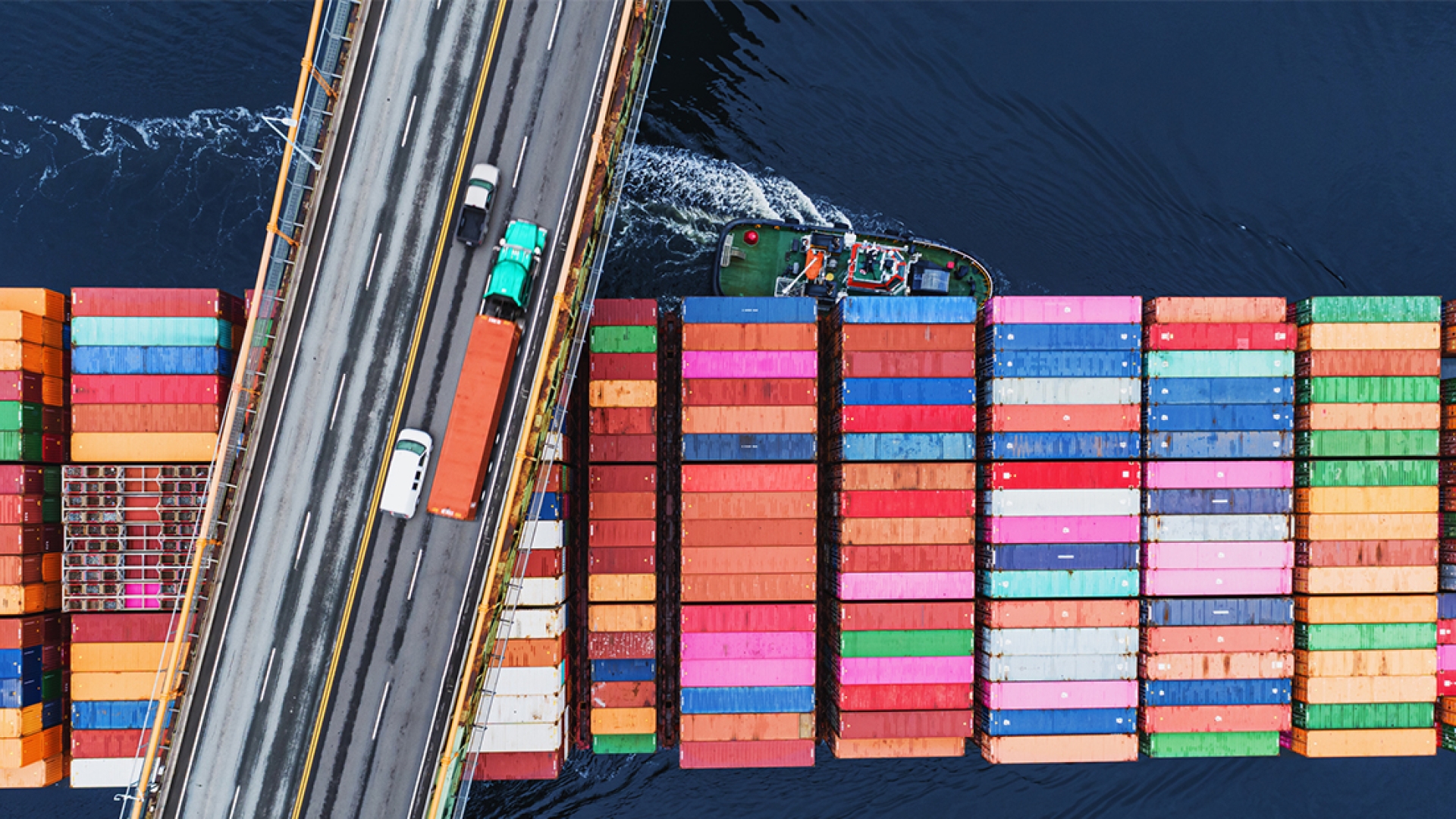
For a long time, it looked like cars with hydrogen engines or fuel cells would one day take over the roads and the transportation sector. Hydrogen fuel cell cars release no harmful emissions of any kind, have a long range, and can be refueled in minutes. In theory they sound like a great way to decarbonize the transportation sector. In practice, hydrogen cars are facing stiff competition from plug-in battery electric vehicles. It has been a running joke in the industry that hydrogen cars are always ten years away.
So, is this the end for the use of hydrogen in motor vehicles? Far from it.
Battery electric technology is great for personal vehicles and selected commercial vehicles in the transportation sector. Meanwhile, the transportation sector includes vehicles with a diverse set of duty cycles and applications. Some of these vehicles and equipment are currently not prioritized for battery electric technology applications. This means hydrogen technology is going to be a part of destination zero carbon emissions for many commercial vehicle operators.
There are two ways to power a motor vehicle using hydrogen. These are hydrogen internal combustion engines (Hydrogen ICE) and hydrogen fuel cells. The first uses hydrogen to fuel an internal combustion engine. The other uses a fuel cell in combination with electric motors and a battery.
Crucially, hydrogen engine drivetrains are mechanically very similar to traditional drivetrains. Hydrogen engine vehicles rely almost entirely on tried and tested components. This means that for risk-averse operators who drive vehicles in harsh environments or who want predictable maintenance costs, they may be the solution of choice. Below are some applications where hydrogen engines are a great option.
Hydrogen engines in construction vehicles and equipment
The construction sector is another source of CO2 emissions. In urban areas, the use of heavy construction equipment can also contribute to lower air quality. This should not be surprising, since a large excavator can consume more than five gallons of diesel fuel per hour. While the battery electric solutions are increasingly becoming viable for smaller excavators, a battery pack large enough to allow a larger excavator to operate for an entire day’s work would need to be quite large. It would also be very expensive.
Meanwhile, compressed hydrogen brings greater energy density. This would allow an excavator to operate with acceptable sized fuel tanks; those that are larger than the ones on traditional diesel machinery yet manageable. These hydrogen engines also eliminate the extended work interruption to recharge batteries.
Hydrogen engines in heavy-duty trucks
Semi-trailer trucks are another category of vehicles where battery electric technology may not be the ultimate decarbonization solution yet.
As with some of the construction equipment, the issue with battery technology comes down to range, reduced cargo space, and charging time. Several manufacturers are developing battery electric semis, but most advertise a range of 150 to 300 miles. This makes them best suited for short- and medium-range haul.
In long-haul transportation, drivers would have to stop for one or two hours to recharge, every three to five hours. Some makers advertise longer ranges, but greater battery capacity can only be achieved at greater cost and with the loss of valuable cargo space.
Hydrogen trucks, in contrast, have a range and refueling time comparable to diesel and natural gas—without any particulate matter or greenhouse gas emissions.
Are hydrogen engines viable without a dense refueling network?
Another reason why all these hydrogen applications are especially promising is that they can be viable without the existence of a dense hydrogen fueling network.
Trucking companies, for example, can plot an itinerary ahead of time using a small number of fueling stations placed along fixed routes, without the need to hunt for fueling stations in the wild. Trucking companies can also install onsite hydrogen dispensing at their regional hubs or distribution centers as well as install electrolyzers to produce hydrogen on site.
Construction sites are another good example for the use of hydrogen engines without a dense refueling network. These sites are stationary, and they are usually functional for months to years where on-site hydrogen storage is more feasible. In the case of a remote construction area, even the possibility of local hydrogen production can be evaluated. Excavators on these sites operate in challenging environmental conditions under aggressive duty cycles. These hard to electrify applications combined with opportunity to store or produce hydrogen locally make hydrogen engines an option for construction vehicles.
Beyond this immediate viability, hydrogen engines also drive the progress in the hydrogen economy and infrastructure.
If these have excited you, don’t forget to read about how hydrogen engines work and their role in reducing vehicle and transportation emissions towards destination zero.
As these commercial applications become mainstream, hydrogen fueling networks will appear to serve them. Conceivably, these limited networks could then be used by personal hydrogen cars. Hydrogen engines are just around the corner, so hydrogen cars may have a shot at revival within less than ten years after all.
Author Profiles
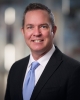
Jim Nebergall, General Manager of the Hydrogen Engine Business
Jim Nebergall is General Manager of the Hydrogen Engine Business at Cummins Inc. and leads the company's global efforts in commercializing hydrogen-fueled internal combustion engines. Hydrogen internal combustion engines are an important technology in the company's accelerated path to decarbonization. Jim joined Cummins in 2002 and has held numerous leadership roles across the company. Most recently, Jim was the Director of Product Strategy and Management for the North American on-highway engine business. Jim is passionate about innovation and has dedicated his Cummins career to advancing technology that improves the environment. He pushed the boundaries of customer-focused innovation to position Cummins as the leading powertrain supplier of choice, managing a portfolio ranging from advanced diesel and natural gas to hybrid powertrains. Jim graduated from Purdue University with a bachelor's degree in electrical and computer engineering. In 2007, he completed his Master of Business Administration degree from Indiana University.
Related Tags