Top 5 reasons hydrogen has a place in the future of rail
By Catherine Morgenstern, Brand Journalist
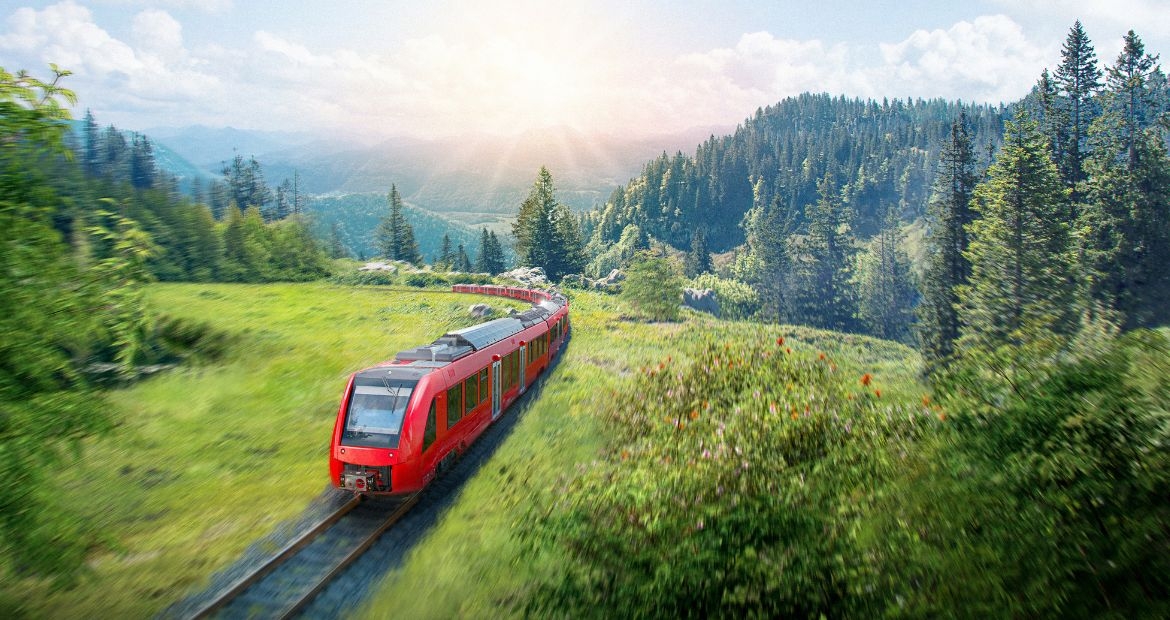
In 2016, Cummins partnered with a European railway equipment manufacturer, to engineer, supply, and integrate the hydrogen fuel cell solution in its trains. The trains entered commercial service in 2018 and can carry up to 150 seated passengers and 150 standing passengers. There is growing interest from several European countries to use the trains for non-electrified tracks.
While many alternative propulsion concepts are still in the development and research stage, hydrogen for rail application is already here. Why has hydrogen been ahead of the curve? In honor of 2021 being named the European Year of Rail, here are five great reasons why hydrogen has a place in the future of the railway industry.
- Trains powered by hydrogen have zero emissions at the point of use. The power required for the train's systems is supplied via a fuel cell, which generates energy by combining the hydrogen stored on the train's roof with oxygen in the air. There are no emissions of carbon dioxide in this process. They are also efficient: fuel cells are up to three times more efficient than internal combustion engines.
- Hydrogen trains can be deployed anywhere and retrofitted into existing trains and lines. The majority of lines across Europe and the U.S., particularly rural lines and lines with little consumer demand, are yet to be converted to carry electric trains. Hydrogen trains represent a cost-effective alternative that doesn't sacrifice efficiency or emissions. They can simply run on existing rail infrastructure without the high cost of adding electrification. Cummins fuel cell solutions are flexible and scalable in their configuration and can be customized to fit customers' needs optimally.
- Hydrogen fuel cell trains have an exceptionally long range of up to 1000 kilometers at a maximum speed of 140km/h between refueling-ten times farther than battery powered electric trains. And refueling is quick: hydrogen powered trains can run for 18 or more hours after less than 20 minutes of refueling.
- Fuel cells are cost effective and low maintenance. The total lifetime cost of ownership is already comparable for trains running on diesel or electrified lines, according to a report by consulting firm Roland Berger. There is a long asset life compared to electrification, and repairs are often as simple as swapping out one plug-in component for another.
- Trains powered by hydrogen are quiet and comfortable. Hydrogen provides a smooth driving experience and emits low noise levels due to the exhaust being only steam and condensed water. This is especially important in urban areas where noise pollution is an issue.
To support the continued expansion of hydrogen fuel systems, Cummins recently announced the ground-breaking of a new facility in Herten Germany to support the production of fuel cell systems for the hundreds of hydrogen trains to be in service over the next several years in Europe. The facility is currently prioritizing the assembly of fuel cell systems, while actively working on expansion plans to support fuel cell stack refurbishment.
Author Profiles
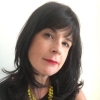
Catherine Morgenstern, Brand Journalist
Catherine Morgenstern is a Brand Journalist for Cummins, covering topics such as alternative propulsion, digitalization, manufacturing innovation, autonomy, sustainability, and workplace trends. She has more than 20 years of experience in corporate communications, holding leadership positions most recently within the Industrial Capital Goods sector. Catherine began her career as a marketing writer for a biotechnology company, where she learned to take complicated and highly technical information and make it accessible to everyone. She believes the concept of "storytelling" is more than a trendy buzzword and loves to find ways for her readers to make personal connections to her subjects. Catherine has a passion for technology and innovation and how its intersection can make an impact in all our lives. Catherine recently moved back to her hometown in the Hudson Valley, New York after a several decades in Los Angeles and Chicago. She is a graduate of UCLA and enjoys gardening and spending time with her husband and three children.
Related Tags